First LEED Gold laurels awarded to the Continental plant in Lithuania
Undoubtedly, the plant of the German corporation Continental is an object that is significant to the history of our state, and two Presidents of Lithuania visited the plant during the relatively short period of its construction. Namely, the outgoing President Dalia Grybauskaitė was present whan the first foundations of the plant were laid; and President Gitanas Nausėda was present at the opening of the plant.
Great importance has been attached to environmental protection: a minimal area is used, lawns are mown, no artificial lawns or plant irrigation systems are used, rain water is collected to water the garden, flowering meadows are seeded and only local plants are used for them; thus, a part of the Lithuanian meadow gene pool is maintained. More than 200 woody plants were planted in the parcel of land and they all are typical of the Lithuanian region: rowans, hornbeams, birches, larches, maples and larches.
National plant
The plant is not a new theatre and it is not even a new national stadium. However, the special attention of both Presidents to the object is justified by the important circumstances, i.e. this is one of the largest plants to be built in a greenfield site. In the place chosen for the territory of the plan, i.e. Kaunas FEZ, the development and the related creation of jobs have dealt with a lot of the social issues and particularly such acute problems as migration. “Continental chose Kaunas for several reasons: first, Kaunas is the main centre of industry, electronics and automation manufacturing in Lithuania. This modern region is abundant in highly qualified specialists, i.e. at least 10 percent of students study Electronics Engineering in Kaunas. Besides this, the region has an appropriate infrastructure. For these reasons, Kaunas seemed to be the ideal place for our new plant,” said Shayan Ali, Manager of the plant, in Lithuania during the open ceremony.

Of course, granting the status of a natural object to the plant is unusual. However, its meaning raises no doubts, as there is a new attitude towards employees who are not just hardworking cogs of the system, but are equal partners involved in the development of the product. The working conditions created in the plant meet the highest standards. The plan of the plant suggests that of flexibly planned premises with conference rooms and a lot of common spaces, namely, a rest space, restaurant and an internal yard have been adapted to meet the leisure needs of the employees. According to the Manager of the plant S. Ali, “this plant was designed and constructed with particular attention to the environment and sustainability. This is the first design of a Continental Automotive plant to which the internationally recognised golden LEED certificate for the employment of sustainable solutions has been granted”. Healthy microclimate conditions, comfortable automated lighting in the workplaces, and cosy work and rest zones have been created for the employees in this building.
The preparation of the design of the Continental plant was entrusted to a young but experienced team from the architectural office StART, run by the Architect Justina Narauskienė. The office was chosen by the main designer of the plant, i.e. Baltic Engineers, which had cooperated with the architects on several occasions in designing other objects.
Design process requires close teamwork
The representatives of the plant also invested a considerable amount of time in the design process. “The customer’s participation in all stages of the design was direct and continuous. During the entire design period, the Project Manager of Continental spent his time in Vilnius, Kaunas and in the central office of Continental in Frankfurt,” said the Architect J. Narauskienė. “The design stage was divided into sections, where each part was approved by the specialists and managers of Continental during creative workshops.”
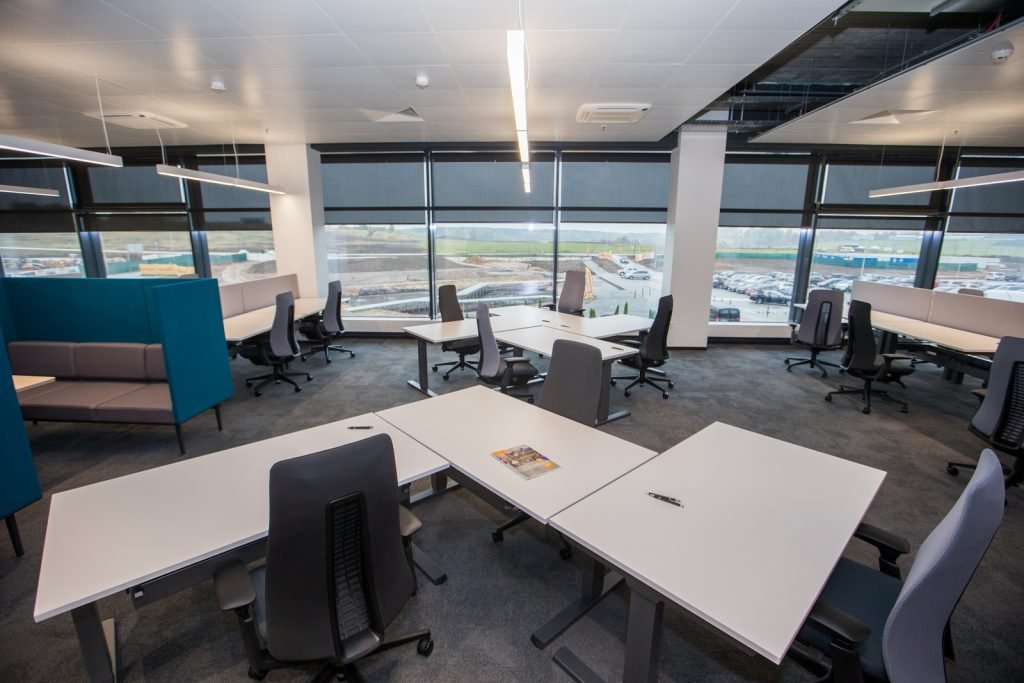
The stages of the architectural part of the design, the design proposals, the technical design and the work design lasted around 8–9 months. Constant teamwork and continuous negotiations for mutual actions and coordination in a 3D environment were carried out with the General Designer of the building, Baltic Engineers UAB. Thus, the design teams had to agree that the work must be carried out within such a short time limit, i. e. some of the design work was carried out in the course of the construction. “It was impossible to avoid corrections,” J. Narauskienė shared her experience. “They were influenced by the optimisation of technological processes, as a prompt response to the customer’s wishes. Production and warehousing zones cover the largest part of the area; thus, we had to meet the technological requirements, the requirements of our colleague engineers and the fire safety regulations. We were able to offer more of our solutions for the administrative part of the building, which had to be met by the designers of the engineering systems.”
The whole design team consisted of around 40 people, including four architects from StART studio, and the following consultants were also engaged: LEED consultants from Poland, i.e. Visio Architects, for the kitchen technologies the consultants of Gastro-projekt PL, FM Global, etc.
High benchmark
Generally, the architectural expression of a plant does not receive considerable attention. What is important is to place all the equipment necessary for technological processes and engineering in a ‘box’ and ensure that the construction process is completed as quickly as possible. Although a ‘brandbook’ straightjacket was created for the Continental plant, the architect has pointed out that they managed to achieve an exclusive and original expression, which was also evaluated by the management of the plant as exemplary in terms of the design of the administrative premises and the main facade.
“Yes, we had the so-called brandbook, which needed to be complied with by all the architects designing Continental. The colour, shape, proportion solutions, and of course the quality requirements, were the most restricted. However, the customer was particularly open to new building design trends, with the modern planning of internal spaces and interior solutions (currently, the Headquarters modern office building is being prepared in Hanover); thus, the benchmark set for us was relatively high.

Although the customer applies its corporative standards (colours, materials, shapes) and quality requirements for all his buildings, he accepted the architects’ proposals concerning the main facade, where the main entrance is formed by a roof of an irregular shape with broken planes oriented towards the square, and the corporate colour was used. Moreover, the architects were absolutely free to interprete the Continental standards in the creation of the interior of the lounge and office spaces, and remained entirely at liberty to create the interior of the restaurant. “The customer clearly declared his position to create the maximum comfort for his employees. We have created internal yards for the use of the employees, which also significantly improve the work environment, with natural lighting in the open space offices,” maintained the architect.
The faceless ‘box’ image has been avoided
The plant has been designed so that an innovative, integrating working environment oriented towards the future needs was created. “As colleagues, we competed with the strong design team of the Hungarian plant, and today we are happy to reveal that the solutions offered by us will be integrated in other new plants being constructed,” said the architect.
The surrounding areas of the plant will not make you to feel as if you have arrived at to some typical ‘technological box’. The project was developed as part of the Greenfield Investment Project; however, during the 8 months of design work and 15 months of construction work, the greenfield parcel has become a fully urbanised territory with a complex of buildings. This not only concerns the engineering infrastructure but also the social infrastructure, public functions, integrated green territory, recreational and sport spaces. All of the internal planning of the parcel of land has not been done in isolation from the surrounding territory. Connections to the cycling routes and bus routes of the city are planned, and the arranged square is an open common space for the dwellers of the surrounding areas.
Impressive ambitions
According to the architect, precise terms of reference for the production and warehousing zones, as well as information on the technical capacity of the equipment and needs, planned employees, logistics and the vehicle flows were received. The design was carried out in accordance with the Continental standards book, the LEED Gold requirements for sustainability of the building, and the more stringent additional fire safety requirements of FM Global. The project and AsBuilt model of the building were created by virtue of the BIM design platform.
The flexible structures of the building are reinforced concrete columns and floor slabs and metal girders. The cover of the roof is made of reinforced concrete plates and a Ruukki profile tin deck. Sandwich type panels, which were also supplied by the representatives of the Finnish concern Ruukki in Lithuania, were used for the walls. The administrative block was built of blocks finished with Ruukki aluminium cassettes. Aluminium facade systems and windows (Reynaers), Clestra display partitions and Rigips plasterboard partitions.
The new plant is in the Kaunas Free Economic Zone, which currently covers a 22 thousand sq. m territory consisting of production, administrative and warehousing premises. All the construction work of the complex added around 23,000 m², so the total volume is about 200,000 m³; the height of the two-storeyed superstructure is about 17 m; and the energy class is A+. 1,200 spaces for employees each day are planned, while the maximum number of persons who can work at the same time is up to 600, and a 200-seat restaurant is also planned for them. The total area of the complex of buildings is around 23,000 m². The main production building with the warehousing premises occupies 22,000 m² including the administrative premises, the area of which is 6,000 m². A 190 parking lot with spaces for electric cars, green cars, car pool spaces, 50 bicycles and 25 motorcycles has been planned. The area of the garden in the internal yard of the administrative building is 400 m² and the area of the green roof is 300 m². A 1 ha square with greenery, an amphitheatre and a rain garden, as well as a sports and training building with a universal open multifunctional sports ground, are arranged in the surrounding areas of the building.
Innovative solutions for the interior and ‘clean’ premises
The main representative spaces are the lounge and the reception desk. All the production staff pass the lounge every day (around 1,200 employees per day) and the guests or future employees of the plant are welcomed here. Rest spaces with a view of the internal yard of the plant are designed for the employees on the ground floor. The production spaces must be ‘clean’ and not accumulate a static charge; thus, an ABP conductive epoxide cover and a SIKA epoxide cover were used, along with large format stoneware tiles, PVC roller coverings and carpeting for the common spaces. Rest and coffee zones with natural light through solarTubes light channels, as well soft furniture were included in the designed for the production space.
The office spaces are also full of multifunctional areas for rest, meetings, training and cooperation; namely, there are meeting rooms and waiting rooms with soft furniture. A ‘show room’ screen with product exposition and a display wall is designed in the lounge. One of the most impressive spaces is a black lobby and stairs. The metal stairs have a cantilever structure. Beneath it, there is a rest space, a coffee zone, and decorative wall designed over two floors of the building. If you climb the stairs, a view to the amphitheatre square opens up.
“We have paid considerable attention to the restaurant in our design, as the customer also considers this function very important. The task was to distance ourselves from the standard-type canteen of a plant,” the architect told us. Thus, a 200-customer open canteen style restaurant with a self-service food line and several ‘pop up’ food islands were designed. We tried to create the broadest range of catering zones from bistro to bar tables, with metal chairs near the food dispensing and passage corridors, ‘casual style dining’ in the family catering hall centre, and restaurant ‘fine dining’ with massive tables, soft furniture and luminaires. Each zone is designed with the square, landscape and the amphitheatre in view. Besides this, a separate zone for heating food was designed. There is a coffee and a dessert zone near the entrance to the restaurant that may be used for informal meetings with colleagues or guests. The space is simple, with a rectangular layout, and with an industrial style concrete ceiling and open engineering, with an acoustic greyish floor. Neutral colours prevail in the interior. The focus is on the views from the display windows into the internal yard and square, where colourful furniture and accessories are in place. The space is divided by different suspended ceilings and suspension lattice structures with plants.
A sustainable public infrastructure has been created
In addition to the internal spaces, the public outside space is also of particular importance. The square designed in front of the main building covers about a 1 ha area. It is divided into different functional areas, with entrances to the building from the car parks, and bus stations are planned.
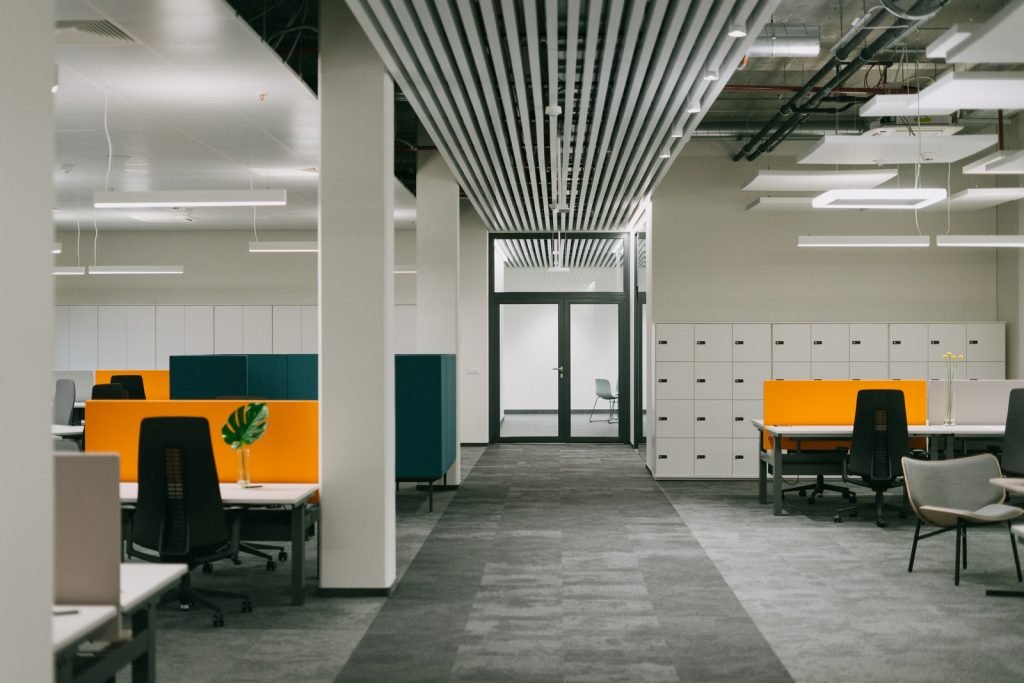
This public space is open to all residents of the surrounding areas, and was designed taking into consideration the customer’s wish to allocate a space to employees for retreating from their work routine and changing the environment. Different rest zones were designated to create shadowed and sunny places. The landscape in front of the building is formed by the amphitheatre square covered with massive granite slabs from Portugal, with the amphitheatre benches, load bearing walls and stairs of diagonal shapes. A representative space is formed with a path to the entrance of the building. The rigid shapes of the building are supplemented by the green ‘islands’ of the prominent relief. Arrays of trees form shadows and help to provide cooler areas on hot summer days. Granite paved walking paths and park paths lead towards the rain garden and rest terrace. Composite wood boards were used in the sunny spaces facing the rain garden.
Rain garden and naturally created ecosystem
The inner garden of the building (400 m²) was created on the basis of forestry principles. The plants were selected and arranged taking into account the amount of light that would be received in the conditions of the closed internal garden. “As the design concept and the LEED requirements state that no artificial irrigation of plants is allowed, special plant species have been chosen,” said J. Narauskienė. A lot of deciduous shrubs, namely, white dogwoods, winged spindles, Anglojap yew and multi-stem birches, were planted. The plants under the trees are composed of the herbaceous plants characteristic of forest areas, ranging from fems to sedges. The inner garden on the second floor (300 m²) was also created as an additional source of natural light and was planted with sedum carpeting. Irrigation systems will not be used for the greenery, plants that grow naturally in Lithuania have been chosen. The hard covers and roofs were designed to intensively reflect the sun rays with a view to avoiding heat islands, and a green roof was designed in one part of the office.
The rain garden is a solution which is very rarely used, and is currently unusual in Lithuania. Water temporarily remains in the garden, but its level fluctuates from drought to standing water. The plants are appropriate and decorative, and the roots of the plants perform a water filtering function. In the blooming meadow environment, trees with ripening fruit are created and this attracts animals ranging from bees to small mammals.
In addition, outdoor spaces for rest, i.e. a sports and training centre, along with a universal sports ground for team games were designed. Open individual sports grounds. No asphalt was used for the outdoor ground cover; instead, only concrete blocks, granite slabs and blocks were used, i.e. materials for intensively reflecting the sunlight were chosen.
Challenges
LEED Gold sets particularly high requirements for the materials used in the building and the territory, even including their colours. Thus, the roof of the building and the majority of the colours in the parcel of land are white or grey. The materials used in the object had to have such certificates as EPH and HPD. Finding trees with such certificates became a serious challenge, since the materials prevailing in Europe had the certificates appropriate for LEED v.3 which did not meet the requirements of LEED v.4.
The architectural and engineering solutions of the building had to not only meet the requirements of STR but also the mandatory requirements of the American design standard ASHRAE, which determines what solutions are not typical of the local market.
In addition, the architects faced the challenges of dealing with the high ground water level, and integrating the building and the infrastructure with the existing situation, so a decision to divide the parcel into terraces was made and the whole area of the production building was maintained on one plane.
“Of course, we had to assess ourselves critically and draw conclusions after the construction work of the building was already finished,” said the Manager of StART studio. “All the construction processes faced their challenges; thus, if it was possible to change something, changes that would simplify the construction processes would be made.”
The project has exceeded expectations
The managers of the plant have welcomed the project and the processes taking place during the construction. “The plant built in Kaunas is a benchmark project for other Continental constructions throughout the world,” said the Manager of the plant S. Ali. “The experience we acquired during the project is already being applied in other new Continental plants in Aguascalientes, Mexico and in Debrecen, Hungary. The plant situated in Kaunas is characterised by the most modern technical cleanliness conditions and meets the highest automotive industry standards.”
The team of architects who passed such an important test of their professional abilities is also satisfied with the results of their work. “We have received very favourable evaluations and comments from the representatives of Continental. Although we created our design in accordance with the standards of the corporation in relation to the quality of the materials and the functions of the premises, the customer has evaluated our project as more distinguished than all other existing plants of the corporation. This was determined by the interior solutions, accents, materials of the administrative part and the layout of the office spaces. When creating the design, we complied with relatively strict rules but, in certain cases, we started to offer our solutions and we are glad that the customer accepted and allowed us to apply these innovations in a very flexible manner. This is probably what distinguished our plant from the other plants,” rejoiced J. Narauskienė.